PULAU INDAH, INDUSTRIAL PARK, Malaysia
Client: Central Spectrum (M) Sdn Bhd
Country: Malaysia
Length of Pipe: 5 km
No. of Valves: 100
Volume of Flow: 30 litres/second
Specialist Feature: Reduced sewer depths through innovative design to negotiate the deep storm water drains
Pulau Indah is an island off the coast of Malaysia, South-west of the capital city Kuala Lumpur. The ground conditions on the island are mangrove swamp overlain with fine sand and a water table approximately 1 metre below the existing ground levels. With storm water drains installed at depths of up to 3 metres, the previously designed gravity system had main sewers 5 metres deep and 4 pumping stations each at a depth of 10 metres from the finished ground levels. With the existing soil conditions, the difficulty and cost of installing the gravity system made it an unattractive solution for the client.
Iseki Redivac designed a vacuum system with the “crossover” pipes from the valve chambers passing through the storm drains at a high level, thereby allowing the main vacuum sewers to be installed at shallow depths. A single vacuum station replaced the four gravity pumping stations by collecting the sewage from the entire development and pumping it directly to the nearby sewage treatment plant. With sewer and chamber depths being considerably reduced, a 40 % capital cost saving was passed onto the client and the single vacuum station significantly reduced the operation and maintenance costs of the local water authority.
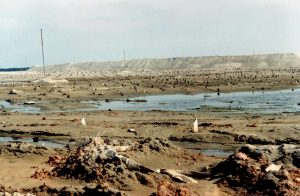
Reclaimed Swamp Land
Vacuum sewers constructed from PN8 polyethylene pipes jointed using electrofusion welding techniques.Vacuum Station Equipment
The two storey station comprises three rotary vane vacuum pumps, a 13.5m³ vacuum vessel and three centrifugal screw sewage discharge pumps.A motor control centre complete with PLC logic controls the M&E equipment automatically and notifies the local water authority when attendance is required at the station via an automatic dial-up facility built within the control centre.
Summary
Iseki’s innovative approach to design overcame the engineering problems caused by the difficult ground conditions and offered a 40% capital cost saving to the client and reduced the operational costs of the local water authority.
Possible Applications for Iseki Redivac’s Technology
Rural community sewerage systems
Industrial developments
Supply bases
Housing development/compounds
Hazardous waste collection
Airports & military installations
Beach developments
Remote villages
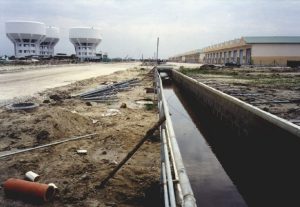
Deep Storm Water Drains
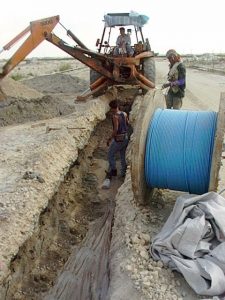
Cable works and trenching
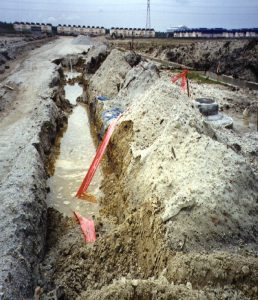
High Water Table
Cost effective solutions to many difficult drainage problems